In late-2007, Heidelberg opened its new
€45 million Wiesloch-Walldorf assembly
hall, measuring 375,000 square feet, to produce
large-format sheetfed presses (Speedmaster
XL 145 and Speedmaster XL 162) in
an effort to eat into the size 6 and 7 market
share controlled by KBA and manroland.
This is a second large-format-sheetfed effort for the company, because back in 1972 Heidelberg
designed and showcased a size 6 Rotaspeed,
but quickly scrapped the project
without making any sort of impact into
Planeta and Roland’s domains.
The original Heidelberg Speedmaster
Classic, in the 40-inch format space,
proved vastly inadequate to cope with the
expanding packaging sector. Sheet sizes
were shrinking from VLG to 3b, which
meant companies like Heidelberg were left
out of the game, watching through the
window. You just could not buy enough
weather stripping and foam to stop the
Speedmaster-Classic’s 10-inch cylinders
from marking.
Heidelberg’s position in the packaging
sector began to change in 1986 with its design
launch of the 3-sided-transfer CD
(Carton Diameter) press line. Now Heidelberg
too had a press that could handle
board. As much as the concept of a 3-sided
cylinder seems avant-garde (Solna originated
this design), the CD was extremely
popular and a big hit for Heidelberg. Trouble-
shooting print issues proved to be
a challenge, however,
as technicians
like to work on even
number transfer
problems, not work
out mathematical
formulations. The
arrival of the CD,
however, buoyed Heidelberg’s business and
went on to be sold en-masse to both commercial
and carton establishments. The
company’s new version 40-inch carton
press, the Speedmaster CX 102, has upgrades
from its flagship XL 106 but retains
CD cylinders and the triple transfer.
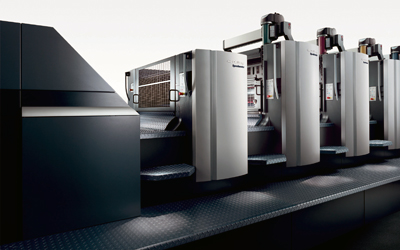 |
Heidelberg’s Speedmaster CX
102, introduced at drupa handle similar substrates
up to 1 mm carton. The CX is the reincarnation of the successful “CD” and
the cousin to Heidelberg’s top line press the XL 106. The XL 106 is designed with
the same cylinder characteristics of Komori, KBA and Roland. The “CX” continues with the double triple transfer same as “CD”. |
Meanwhile, Mitsubishi expanded its
portfolio to add a designated carton press,
called the FC, which would not run paper,
just board, and there were several variants
up to 1 mm that a printer could purchase.
Along with the 3b, Mitsubishi extended its
range to include slightly oversized size 5
and 6 versions. Most of these machines
were also destined for carton plants.
Komori was not sitting around doodling
either and in 1981 launched its Lithrone series.
This press incorporated many good
bits of design like unit construction, double-
size cylinders, robust frames and a sheet
transfer thickness up to 0.8 mm. The
Lithrone 40 also evolved into 44- and 50-
inch versions. To better understand the impact
of Komori’s design, many of the
features implemented by Japanese press
maker back in 1981 are now being employed
on the presses of competing vendors.
These Komori presses are right at
home hammering out carton just like the
others I’ve mentioned.
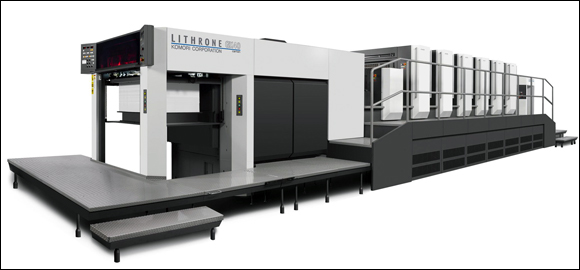
Komori Lithrone GLX - The design concept of very large impression and
transfer cylinders is key and the heart of a packaging press. The In-feed
design and delivery low downs that are beefed up for heavy
stock, are also important attributes Planeta was the trailblazer in design of the large cylinder
and skeleton transfer design, beginning in
1965. Today every manufacturer has these designs to some
extent. Beginning in 1981, Komori was the first
company after Planeta to build presses this way. The GLX has specific improvements that allow for
all types of board to run with ease.
manroland, following its early-2012
reincarnation, remains visible in 3b to size
8 (700 and 900 series machines). manroland
had owned the carton business at
one time. Looking back at the Roland days
its major challenge was losing out on price
to Planeta. Anyone in this business will tell
you its mighty difficult to claw back market
share. But again, with the advances in
sheetfed technology reaching a near-universal
crescendo, manroland’s presses are
in-line with the successful designs KBA and
Komori established in the early-1980s.
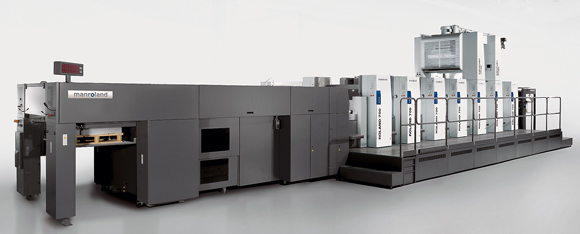
manroland ’s ROLAND 700 HiPrint HS is
designed for producing packaging and like Komori commercial work too.
It features the same double-double impression and transfer
design as the Komori , KBA and Heidelberg.
More than one kind of apple
Looking over modern press designs, I
cannot see a definitive winner in today’s
carton-press debate when it comes to 40-
inch machines (with the major press
makers actually building 41-inch formats).
Today, any one can provide a press
ideally suited for packaging. Besides some
variances in options, including some that
are unique to each manufacturer, the
field is more level today than at anytime
in our recent past.
Throughout modern times, especially
in the world of print, many decisions are
made without regard for real facts. They
are driven instead by visual and sensory
perceptions that are seized upon and exploited
by the folks making and marketing
the equipment you buy.
In China and India, the shear terror of
buying a perfecting press is a great example.
Press doctrine, which usually starts at
the supplier level, wicks its way down to
the user and suddenly an opinion becomes
fact. In India, for example, there
are companies that would even pull out
the pincer from a Speedmaster and insert
a homemade gripper bar in its place, so
deep was the conviction
that perfecting
machines
were the road to
ruin in straightprint
applications.
India remains to
this day a strong
user of the older
Planeta Variant
presses because they are cheap and do
not mark nearly as much as a 10-inch
Speedmaster Classic. Developing countries
like India were not able to buy CD
and Lithrone presses in the used market
because of lack of supply and high prices.
Not until these countries started to
grasp the long perfector did they change
their views on perfecting. Excuses were always somewhat
factually based and that is what gave
relevance to the mindset. True – a perfecting
press is complicated and more expensive
to maintain, but not to the extent
of removing it.
Just like politics and religion, no single
press owns the total solution. There are
enough crises and flair ups to prove that
the world around us cannot find common
ground by separating fact from fiction.
In our world of machinery,
however, talking rationally about different
ideas can lead to
proper benchmarking conclusions where
everyone can work from fact.
Printers and suppliers alike can become
so blind-sighted by stories and
skewed history lessons that we sometimes
fail to consider what is true. With cartonmachine
buying decisions, it is much
more important to understand a supplier’s
level of after-sale service or the real
costs of ownership, before deciding on all
their press features. There are certainly
divisive and justifiable reasons for choosing
one press over the other, but it is just
wrong to assume any one manufacturer
owns today’s folding-carton podium.
|