The millennium Drupa 2000 trade fair was electric. World economies had just come off the best five years of steady growth, and the internet was only beginning its attack on analog commerce. At Drupa, Komori Corporation showcased a brand new press: the Lithrone S40 Project D. The D stood for Digital. A few years prior, Heidelberg had invented the same hybrid press in the 29-inch SM74-DI. Now, for the first time, a B1 40-inch press was on offer.
By the end of 2001, a six-color was sold in Canada but unfortunately (for Komori) into one of the largest Heidelberg plants. I remember it well, and on one visit I spoke to the operator about how he liked it. “We call it Project Downtime” was his response. Struggle they did. Mostly because the general operating procedures were completely different but in reality, it wasn’t the press at all. It was the tethering of two new technologies – Creo’s Square Spot direct imaging heads on a traditional offset press. Heidelberg’s SM74-DI ran into the same problem, and eventually, most of the expensive Creo heads were removed, and SM74’s turned back into regular offset presses.
|
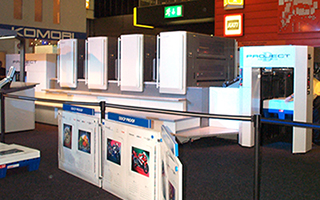 |
Komori Project "D" introduced at Drupa 2000 |
In 2000, everyone in the Print communication industry was abuzz with Computer-To-Plate imaging. CTP devices (both violet and thermal) were being installed faster than any hardware previously invented. But, installing the same imaging unit on a six-color press meant you had in effect, six CTP devices. Even without early teething problems, what looked like a logical next step in press efficiencies turned out to be a bust.
Revolutionary? Yes. Too soon? As it turned out, it was. Add in the recession of 2000/2001, and it all conspired against what seemed like a great idea.
I’m always fascinated by how we make decisions. Reaching into the past offers us the opportunity to develop a sense of how the future turned out and spotted the human mistakes we make.
In 1926, Vogtlaendische Maschinenfabrik A.G. in Plauen Germany produced what they said was the world’s first four-color offset press. Running at an astounding 2,200 sheets per hour, this seemed revolutionary and made logical sense too. Soon the market was full of press builders' offering similar technologies. This made sense. As we already had two color presses and a four-color was simply evolutionary.
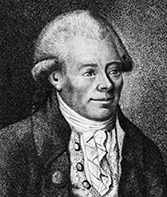
|
In 1778, from the mind of Georg Christoph Lichtenberg, a German scientist, came upon a new technology that would come to be known as electrostatic printing. Coating paper with zinc oxide and applying an electrostatic charge could create an image.
By 1961, the A.B. Dick Co. in Chicago had built an addressing machine for Time Inc. that could lay down 20,000 characters per second on narrow rolls of specially coated paper. That’s only 183 years later! Lichtenberg was also considered the father of what would become ISO 216 and standardized paper sizes in most of the world, except Canada and America, in use today.
|
« Georg Christoph Lichtenberg |
|
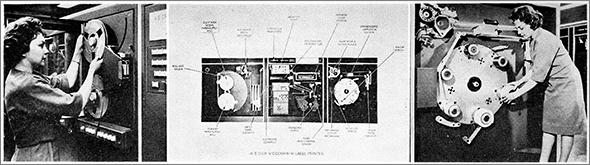
High-speed electronic printing system developed by A.B. Dick, for Time Inc., called the Time Videograph. The technology allows for processing and printing of a large amount of data, as well as last-minute updating of subscriber data. The system is capable of printing 260,000 labels per hour.
|
In 1964, America’s Harris-Intertype and Mead went further and designed a larger roll-fed press that could print military maps at the rate of 2,000 five-color images per hour. The printing industry was hungry to implement new technology, and Electrostatic [printing] looked like the golden goose. It wasn’t, or it was simply too early. Chester Carlson’s experimentation with Xerography was still in its infancy but would finally prevail with symbiotic applications. |
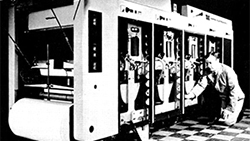 |
Harris-Intertype's electrostatic map printer » |
Harris moved on for offset was its bread and butter, and Harris had just recently received their largest order ever with a USD3.4 Million press order from Western Publishing in Racine, Wisconsin. That’s USD28.5 Million in today’s money and a heck of a lot of Golden Books! Keep in mind, those presses had no consoles, electronics, plate-loading or other labor-saving devices. They probably were only supplied with ink agitators as an option.
The National Lithographer’s January 1964 article, Looking Ahead in The Graphic Arts Industry, tried to “guess” what the Print world would like in the future. Their ideas stemmed from a new sector – Electronics. Spurred by the recent mass production of the transistor, great minds were day-dreaming about how they “assumed” new tools would produce more [Print] at less cost and higher quality. Surprisingly, some did come to pass. Most did not.
Talk of an exposed plate from film without using a camera was only a dream. Neither the concept of reducing film flats to 2-inch microfilm rolls nor then imaging (projecting) directly to a special plate on the press went anywhere.
Another one I remember hearing a lot about was the so-called one-shot skid printing concept. Take a flat (film), place it on top of a skid of paper and fire X-rays through the film to transfer the images through the full skid.
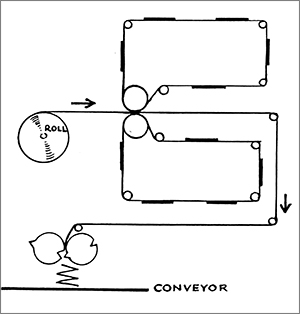 |
Finally, the idea to eliminate perfect binding by placing glue along the gutters of a signature during folding. Once folded into a signature the section is already bound. What about the whole book?
Some ideas did materialize such as the automated proof-reading for one, and optical scanning of MICR codes was another.
Single-Pass Belt Printing did make in-roads. An early Canadian printer, Stroud, Bridgeman Press of Toronto, helped develop this idea whereby plates are mounted on an endless belt and could conceivably print an entire book in one revolution. The Cameron Belt Press came out of this and for a short time advanced – even being linked directly from its folder to a perfect binder. Most Bingo sheets were also printed in large volumes.
|
« Single-pass belt printing |
Even though technology is constantly changing, one thing seems to never alter - our inability to see the future. Man looks at tomorrow’s challenges and tries to improve on them with today’s prejudicial technology.
Truly amazing leaps in digital platforms are upon us right now. HP’s recent launching of the PageWide C500 corrugated inkjet press which can produce a massive 246 linear ft/min (75 linear m/min) will drive more business away from offset. Xerox’s Iridesse™ six-color, CMYK and two additional extra colors including metallic gold and silver, will reach further into the short-run market with a reasonable 120 pages/min output. Let’s not forget the Landa system – which similar to HP’s Virtual Belt Technology (VBT) is coming. Every inkjet or toner manufacturer is actively launching faster and better platforms right now.
|
Even though technology is constantly
changing, one thing never alters:
Our inability
to see the future. We look at tomorrow’s
challenges and try to improve on
them with today’s prejudicial technology. |
|
|
With the rapid change from Offset to any type of Digital device, best not make hard decisions about tomorrow but instead take advantage of what's on offer today.
|